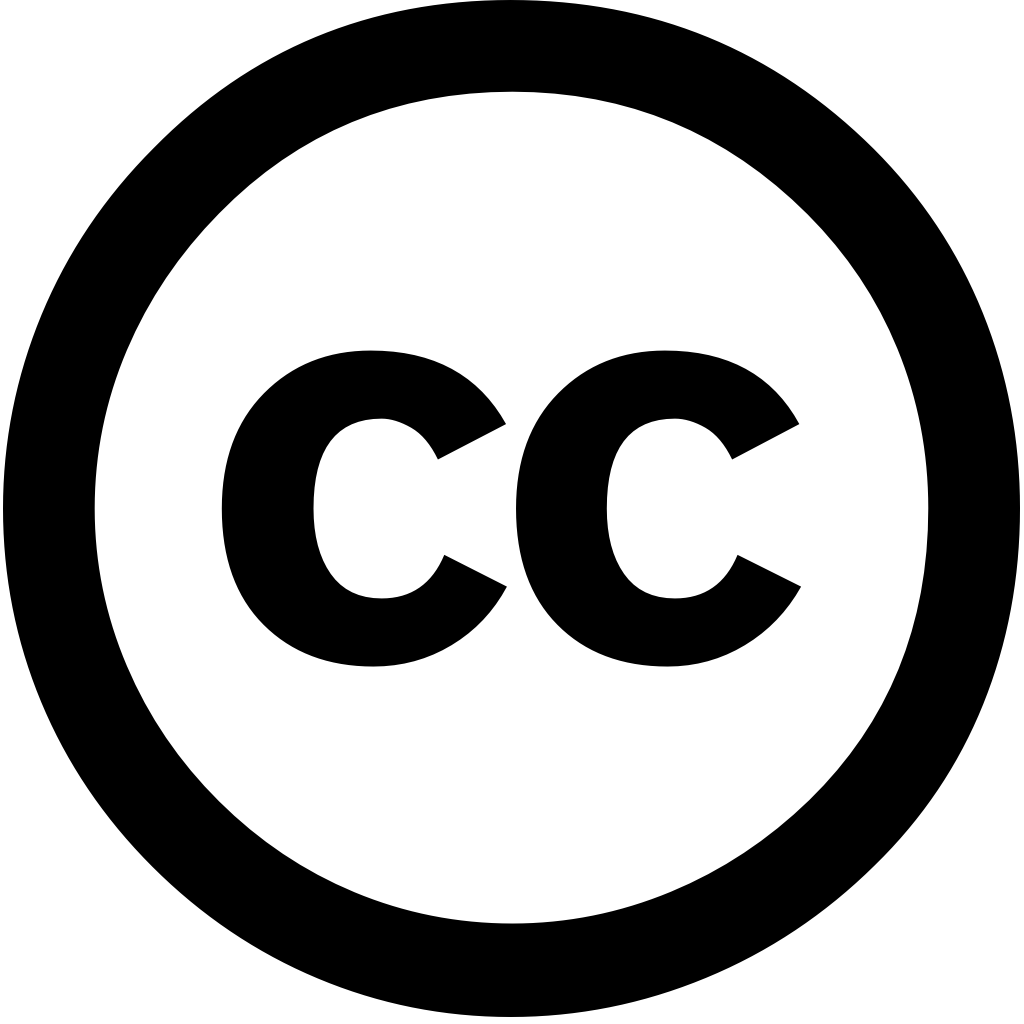
Case Studies in Thermal Engineering, Год журнала: 2024, Номер unknown, С. 105552 - 105552
Опубликована: Ноя. 1, 2024
Язык: Английский
Case Studies in Thermal Engineering, Год журнала: 2024, Номер unknown, С. 105552 - 105552
Опубликована: Ноя. 1, 2024
Язык: Английский
The International Journal of Advanced Manufacturing Technology, Год журнала: 2024, Номер unknown
Опубликована: Июнь 19, 2024
Язык: Английский
Процитировано
24Ships and Offshore Structures, Год журнала: 2024, Номер 19(12), С. 2190 - 2203
Опубликована: Март 21, 2024
This research scrutinizes and contrasts the crashworthiness of single-core two-core corrugated sandwich panels with varying configurations, influenced by crucial parameters like thickness, core angle, foam filling. Experimental investigations encompass quasi-static compressive loads low-velocity impact tests on these structures. Employing design experiment (DOE) method, study examines parameter impacts initial peak crushing force (IPCF) specific energy absorption (SEA) across three sequential steps. The fabrication phase involves creating square trapezoidal aluminium bonded using specialized glue. results notably highlight pivotal role panel thickness in enhancing crashworthiness, displaying a direct correlation between responses. Particularly, configurations exhibit superior performance reducing IPCF during loading compared to other panels. These structures showcase exceptional capability diminishing rates loading, surpassing even foam-filled demonstrating among tested configurations.
Язык: Английский
Процитировано
13Biomass Conversion and Biorefinery, Год журнала: 2023, Номер 14(23), С. 29265 - 29282
Опубликована: Сен. 4, 2023
Язык: Английский
Процитировано
14Applied Engineering Letters Journal of Engineering and Applied Sciences, Год журнала: 2024, Номер 9(2), С. 64 - 75
Опубликована: Янв. 1, 2024
The present study aims to assess the impact of alfa and date palm natural fibers as reinforcement for epoxy, vinyl ester, polyimide polymer (Alfa-Date palm/epoxy, Alfa-Date palm/vinyl Alfa-date palm/polyimide) through a genetic approach. employs simulation rooted in Weibull formalism, employing operators such selection, crossing, mutation nuanced evaluation damage at fiber-matrix interface across studied materials. algorithm results authentically capture intrinsic behaviour these materials, emphasising key mechanical properties like Young’s Modulus, deformation, stress break. obtained highlight that matrix showing highest modulus value its fiber- exhibits superior strength. These conclusions align with contemporary advancements fiber-reinforced composite materials tailored diverse industries eco-friendly applications.
Язык: Английский
Процитировано
4Mechanics of Advanced Materials and Structures, Год журнала: 2024, Номер unknown, С. 1 - 20
Опубликована: Авг. 8, 2024
This study explores the flexural behavior and free vibration analysis of sandwich plates including natural fiber-reinforced polymer composite faces Polyethylene Terephthalate (PET) foam cores under a range edge situations. ABAQUS is used to do numerical simulations with three-dimensional solid elements (C3D8R). To ascertain frequencies plates, experimental procedures such as impact hammer testing Fast Fourier Transform (FFT) are carried out. The inference different geometrical parameters on investigated through simulation in ABAQUS. gives brief outlines regarding for engineering applications.
Язык: Английский
Процитировано
4Composites Part C Open Access, Год журнала: 2025, Номер unknown, С. 100564 - 100564
Опубликована: Янв. 1, 2025
Язык: Английский
Процитировано
0Rapid Prototyping Journal, Год журнала: 2025, Номер unknown
Опубликована: Фев. 7, 2025
Purpose The purpose of this study is to investigate the bending behaviour three-dimensional (3D) thermoplastic polyurethane (TPU) structures printed onto fabric. Design/methodology/approach TPU parts with varying infill patterns and raster angles were 3D-printed both woven knitted fabrics. resulting hybrid structures’ behaviours evaluated using three test methods: cantilever bending, three-point circular compression. Besides, sides tested capture influence direction. Findings fabric structure effective on adhesion force greater values observed for structures, angle directions structures. 45° resulted in resistance methods. For gyroid generally exhibits superior resistance. A case fabricating a personal elbow brace cubital tunnel syndrome was also introduced. Originality/value This provides experimental information about effects 3D printing parameters supports development special-purpose designs tailored functionalities various applications.
Язык: Английский
Процитировано
0Polymer Composites, Год журнала: 2025, Номер unknown
Опубликована: Фев. 17, 2025
Abstract Sandwich structures are crucial in automotive, and construction industries due to their lightweight, high‐strength properties, insulation, energy absorption capabilities. In addition, 3D‐printed sandwich important customizable geometry controlled material distribution, which enhance strength stiffness. This study examines the mechanical properties of composite with a honeycomb core. The skin, fabricated using wet hand lay‐up method, consists glass, carbon, epoxy resin, while fused deposition modeling machine produces polylactic acid (PLA+) A full factorial design analysis variance were employed evaluate effects skin core orientation on through compression three‐point bending tests. performance improved core‐skin synergy, enhancing load distribution resistance. Carbon/epoxy skins offered stiffness strength, delaying failure modes, glass/epoxy provides flexibility cost‐efficiency. Hybrid combined these benefits, stability. vertical further maximized capacity minimized buckling compared horizontal alignment. Optical revealed crack propagation as primary mechanisms. Last but not least, finite element ABAQUS confirmed qualitative similarity load–displacement curves deformation behavior experimental results. Highlights Mechanical analyzed via experiment. Vertical improves compressive flexural over cores. deliver superior panels. Failure mechanisms include buckling, cell wall debonding, wrinkling/cracking. Finite results closely aligned tests, validating structural predictions.
Язык: Английский
Процитировано
0Multiscale and Multidisciplinary Modeling Experiments and Design, Год журнала: 2025, Номер 8(6)
Опубликована: Апрель 19, 2025
Язык: Английский
Процитировано
0Materials & Design, Год журнала: 2024, Номер 243, С. 113069 - 113069
Опубликована: Июнь 5, 2024
A modified Miura foldcore geometry was developed by introducing sub-folds into the cell walls of a conventional foldcore. Similar to other sub-fold foldcores, stable plastic hinge lines were generated at sites under guidance and transformed traveling or stationary in subsequent crushing process. Therefore, comparison foldcore, dual-sub-fold exhibited higher average force with an improvement 60.8 % optimum case. The relatively lower stiffness sites, effectively reducing initial peak force. This reduction reached maximum decrease 70 %. Moreover, this glued two parallel rigid plates (top bottom), making it more suitable for engineering applications. parametric study indicated that predictable deformation modes. It found could be enhanced core folding angle, elevating position, decreasing size, elongating theoretical model predicting energy absorption performance also established.
Язык: Английский
Процитировано
3