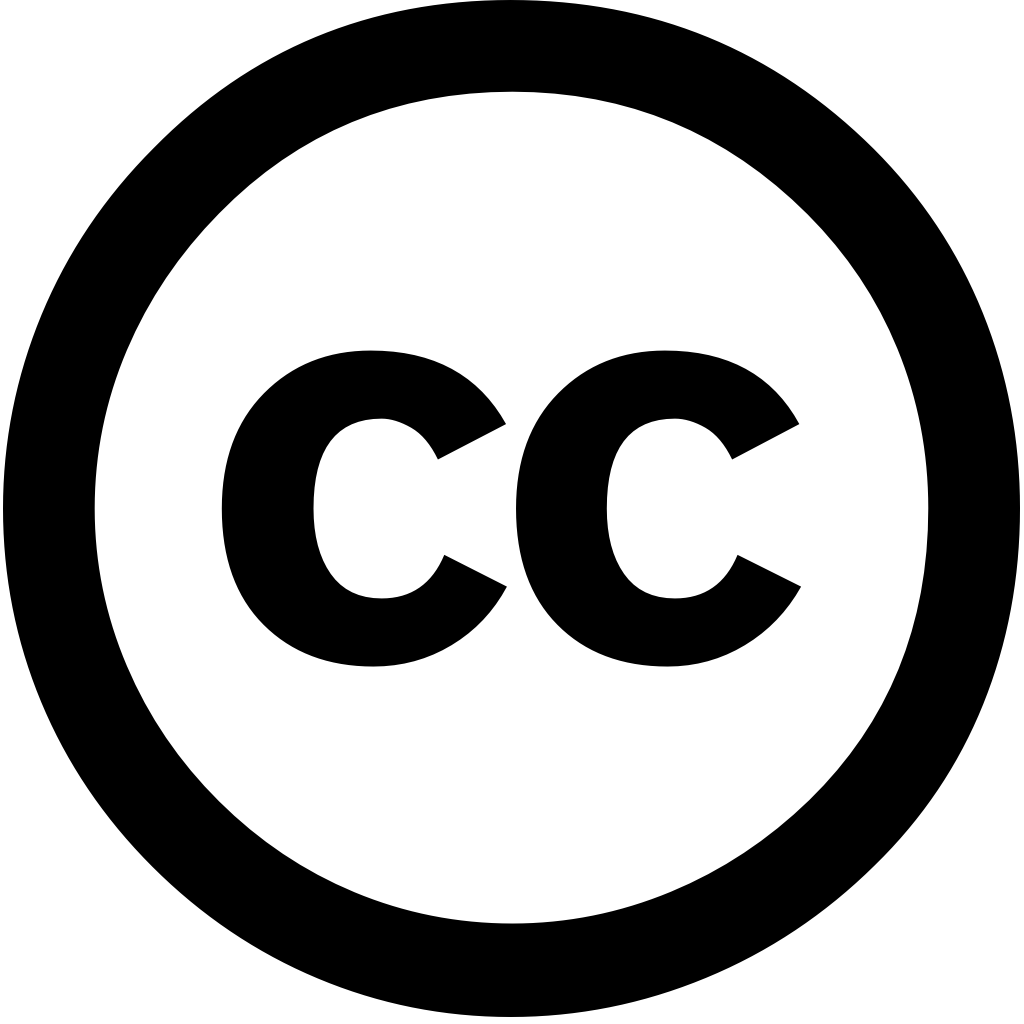
Journal of Materials Research and Technology, Journal Year: 2024, Volume and Issue: unknown
Published: Nov. 1, 2024
Language: Английский
Journal of Materials Research and Technology, Journal Year: 2024, Volume and Issue: unknown
Published: Nov. 1, 2024
Language: Английский
Journal of the Mechanics and Physics of Solids, Journal Year: 2024, Volume and Issue: 185, P. 105570 - 105570
Published: Feb. 12, 2024
Language: Английский
Citations
11Advanced Engineering Materials, Journal Year: 2025, Volume and Issue: unknown
Published: April 28, 2025
Knowledge of alloy recrystallization is key to optimizing microstructures and achieving superior material properties. Computational models predicting microstructural evolution during significantly enhance control microstructure formation manufacturing. Accurate prediction parameters, including fraction grain size, highly desirable. However, developing robust under various processing conditions remains an active research area. Herein, using interstitial free‐steel for simulations experiments, plastic deformation polycrystalline simulated a physics‐based crystal plasticity model. A real serves as the initial configuration. The resulting inhomogeneous dislocation density distribution deformed topology are used in multi‐phase‐field simulation recrystallization. In primary recrystallization, nucleation strongly influences kinetics final microstructure. model, predicts both number positions nuclei. Comparing simulations—one considering other assuming constant random seed positioning—demonstrates importance heterogeneous distribution. Results confirm that static simulations, accurately reflecting utilizing driving force growth nucleation, can be successfully performed proposed
Language: Английский
Citations
1Journal of Materials Research and Technology, Journal Year: 2024, Volume and Issue: 30, P. 40 - 51
Published: March 12, 2024
In this study, an integrated crystal plasticity and cellular automaton (CA) model has been developed employed to investigate the processes of cold rolling annealing in ferritic stainless steel. Crystal simulates deformation microstructure, texture corresponding dislocation density distribution rolled Meanwhile, CA predicts microstructural evolution originating from nucleation growth. The resolution improved using a newly remeshing technique, which allows for capture grain substructure microstructure. validated by experimental measurements with electron backscatter diffraction (EBSD) terms comparing orientation functions (ODFs), misorientation, local substructures, size. good agreement between simulations experiments indicates that is reliable efficient predicting microstructure evolutions during subsequent annealing.
Language: Английский
Citations
4Rare Metals, Journal Year: 2025, Volume and Issue: unknown
Published: Jan. 31, 2025
Language: Английский
Citations
0International Journal of Machine Tools and Manufacture, Journal Year: 2025, Volume and Issue: unknown, P. 104268 - 104268
Published: March 1, 2025
Language: Английский
Citations
0Metals, Journal Year: 2024, Volume and Issue: 14(11), P. 1230 - 1230
Published: Oct. 28, 2024
The evolution of microstructures during the hot working metallic materials determines their workability and properties. Recrystallization is an important softening mechanism in material forming that has been extensively researched recent decades. This paper comprehensively reviews basic methods applications numerical simulations dynamic recrystallization (DRX). advantages shortcomings simulation are evaluated. Mean field models used to implicitly describe DRX process embedded into a finite element (FE) program for forming. These provide volume fraction average grain size FE results without requiring extra computational resources. However, they do not accurately microphysical mechanism, leading lower accuracy. On other hand, full explicitly predict topology on mesoscopic scale, fully considering microscopic physical mechanism. enhances accuracy but requires significant amount Recently, coupling with polycrystal plasticity precipitation rapidly developed, more influencing factors microscale. Furthermore, integration evolving machine learning potential significantly improve efficiency simulation.
Language: Английский
Citations
2Journal of Materials Research and Technology, Journal Year: 2024, Volume and Issue: 32, P. 23 - 36
Published: July 23, 2024
In order to improve the plasticity of titanium alloy welded joints, relevant scholars currently focus primarily on studying mechanism action alloying elements Mo and V, such as reducing phase transition temperature seam ensuring a certain amount β residue in seam. addition improving stability strengthening ability joint, it can also maintain degree joint. However, poor impact toughness is still key problem that restricts its long-term stable service harsh environment. Our work designed developed new Ti–Al–Cr–Mo–Zr solid welding wire, with synergistic effect Al, Cr, Zr, microstructure grain be refined while enough stiffness wire flatness during feeding into designated working area. It ensures good wetting spreading flow performance liquid molten pool metal process, so better formation obtained. The relative contents α′ martensite are 76.79% 23.21%, respectively. residual interspersed between slats. provides path for plastic deformation making easier dislocation slip pass β/α′ interface. At same time, more channels small number fine twins found interior martensite, which ensure strength taking account toughness. After testing, average tensile joints 901 MPa, close 95% base (BM), post-fracture elongation 21%, value at room distributed 25 J 33 J, meets requirements joint suitable Ti64 structure under conditions.
Language: Английский
Citations
1Engineering Failure Analysis, Journal Year: 2024, Volume and Issue: 167, P. 109062 - 109062
Published: Nov. 9, 2024
Language: Английский
Citations
1Journal of Alloys and Compounds, Journal Year: 2024, Volume and Issue: unknown, P. 178149 - 178149
Published: Dec. 1, 2024
Language: Английский
Citations
1Published: Jan. 1, 2024
Fracture at interface causes plastic deformation in the vicinity region. Conventional energy dissipation theory indicates that ductile toughens by absorbing energy. However, microstructure directly affects local deformability and fracture behaviour, implying a more complicated toughening mechanism. In this study, effect of hardness on behaviour Fe/Ni was investigated. By experimental approach, interfaces with without dynamic recrystallization (DRX) were fabricated controlling bonding conditions. It showed compression-induced is main source hardening vicinity. Moreover, hardened DRX vicinities exhibited improved toughness, which inconsistent to theory. To clarify observation, crystal plasticity FEM (CPFEM) approach employed distinguish effects interfacial microstructure. The result although higher absorbs dissipated energy, severe stress concentration leads early poor toughness. On other hand, DRXed grains disperse distribution provide potential sub-crack sites. A combined uniform responsible for toughness grains.
Language: Английский
Citations
0