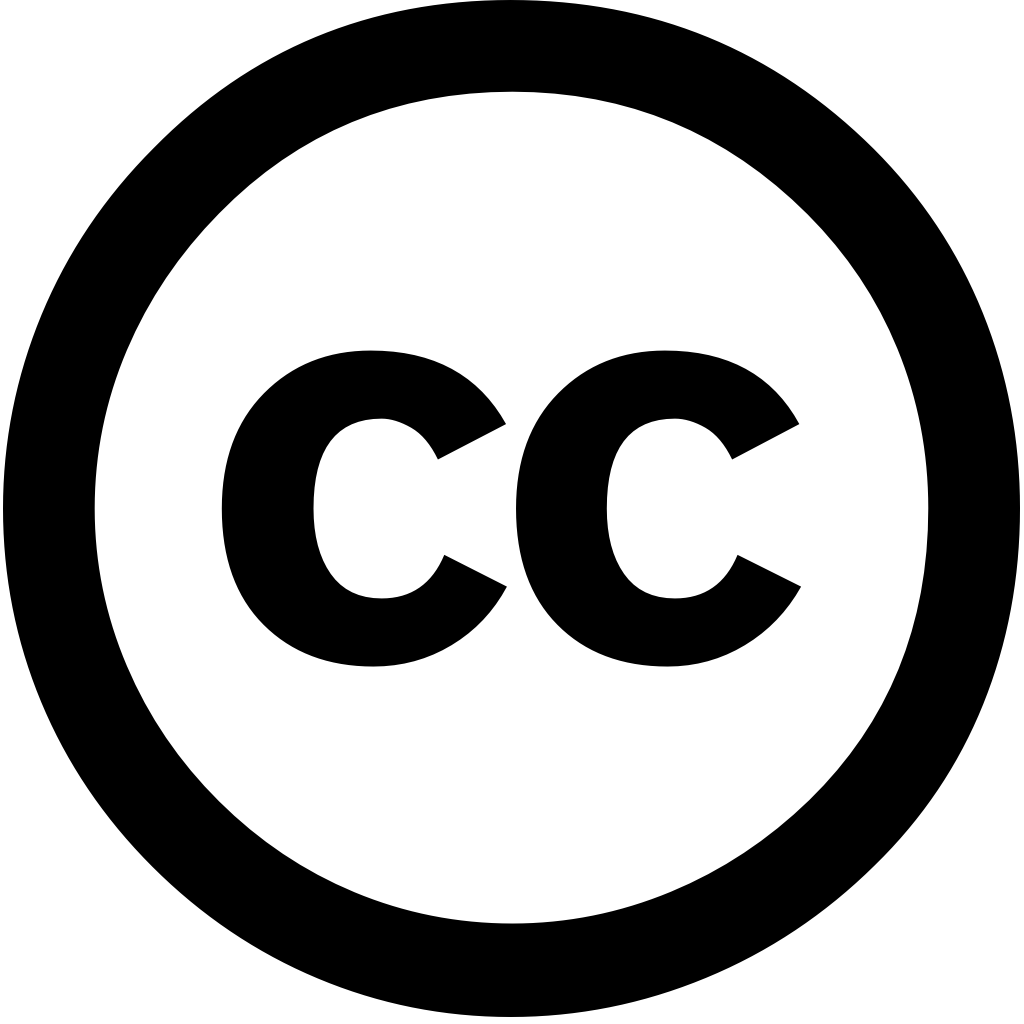
Matéria (Rio de Janeiro), Journal Year: 2024, Volume and Issue: 29(4)
Published: Jan. 1, 2024
Language: Английский
Matéria (Rio de Janeiro), Journal Year: 2024, Volume and Issue: 29(4)
Published: Jan. 1, 2024
Language: Английский
Polymer Composites, Journal Year: 2024, Volume and Issue: 45(10), P. 9421 - 9439
Published: April 9, 2024
Abstract This study investigates the influence of NaOH treatment on tribological behavior in hybrid fiber‐reinforced composites, specifically employing Banana fiber with Al 2 O 3 filler an epoxy matrix. Through design experiments (DOE), disc speed, wear duration, and are analyzed for specific rate (SWR) coefficient friction (COF). To advance understanding characteristics, leverages advanced machine learning, using Python‐powered artificial neural networks (ANN), is integrated innovative ANN hyperparameter optimization. Optimized parameters (1050 rpm, 60 s, 5% treatment) significantly minimize SWR (12.38 × 10 −5 mm /Nm) COF (0.2). Scanning electron microscopy (SEM) analysis reveals improved interfacial adhesion identifies micro‐cracks as primary mechanism. work contributes to a profound offering fine‐tuned predictive model optimizing advancing material science engineering. Highlights Reduced SWR, composites via DOE: Explored impact. Advanced learning techniques enhanced prediction. Innovative: Optimal Parameters: 1050 treatment.
Language: Английский
Citations
17Polymer Composites, Journal Year: 2025, Volume and Issue: unknown
Published: Jan. 13, 2025
Abstract The investigation focused on the glass fiber‐reinforced polymer (GFRP) composite co‐cure single lap joint (CC‐SLJ) that incorporates graphene nanoparticles (GNP) in epoxy and carbon (CFRP) Z‐pin reinforcement. flexural test indicated integration of GNP CFRP‐Z‐pin within inner outer layers SLJ leads to improvement strength. strength CC‐SLJ reinforced with GNP/epoxy reinforcement reaches 145.02 MPa under static loading, an 69.55% over unreinforced SLJ. loading incorporated demonstrate a significant 150.34 MPa, 71.22% Fractography revealed incorporation Z pins into enhances interfacial bonding between adhesive adherend, increases surface roughness, improves pin pull‐out resistance, influences crack formation. Highlights technique is used fabricate single‐lap GFRP joints. Carbon adhesive. was higher 1.25 wt% 2.5 vol% 90°/Z‐pin. Multiple reinforcements achieve its maximum Failure analysis conducted using microscopes FESEM images.
Language: Английский
Citations
2Journal of Natural Fibers, Journal Year: 2024, Volume and Issue: 21(1)
Published: Jan. 25, 2024
The research conducted focused on examining the unique properties of Agave Americana Flower Stem fiber (AAFS), particularly its behavior under quasi-static tensile conditions. A total 200 AAFS fibers were subjected to tests using a standard gauge length 40 mm. Tests spanned seven groups with quantities (N) ranging from 30 200. study aimed understand fibers' mechanical traits, as resistance and modulus elasticity, see how different test influence these properties. significant observation was dispersion characteristics fibers, common trait natural fibers. To this, we applied rigorous statistical tools, including Weibull distribution at 95% confidence interval one-way ANOVA. mathematical model produced utilizing data experiments regarding ANN provided correlation coefficients (R2) 0.9897, 0.9971, 0.9993, 0.9939 for training, validation, testing, all datasets respectively, which able accurately predict experimental data. proposed would be tremendous assistance engineers designers in obtaining green composite materials that are based thereby more durable. These methods illuminated patterns our results, enriching understanding mechanics.
Language: Английский
Citations
14Fibers and Polymers, Journal Year: 2024, Volume and Issue: 25(8), P. 3115 - 3133
Published: July 19, 2024
Language: Английский
Citations
10Journal of Adhesion Science and Technology, Journal Year: 2024, Volume and Issue: unknown, P. 1 - 28
Published: Nov. 4, 2024
Among the diverse adhesive-bonded joining methods, co-curing technique offers several advantages for fusing structural components. Co-curing effectively enhances specific strengths and ensures more equitable stress distribution. This research investigated multi-walled carbon nanotubes (MWCNTs) incorporated with varying wt.% in fibre-reinforced polymeric (CFRP) composite joints through co-cure bonding techniques. The effects of flexural vibration behaviour CFRP were evaluated using three-point bending free tests. Experimental results revealed that epoxy adhesive containing 0.5 nanofiller demonstrated highest strength modulus. These values significantly superior to pure adhesive, exhibiting increases 270 120%, respectively. However, 1.0 exhibited maximum natural frequency under three modes, which is 29, 17, 14% higher than adhesive. statistical analysis was examined an ANOVA, ensuring reliability findings. Optimisation prediction done Levenberg-Marquardt artificial neural network, further reinforcing confidence outcomes. overall coefficient (R) mean square error 0.99844 within acceptable range, indicating both outcomes are reliable agreement.
Language: Английский
Citations
9Nanotechnology Reviews, Journal Year: 2024, Volume and Issue: 13(1)
Published: Jan. 1, 2024
Abstract Co-curing bonding is more efficient than co-bonding and secondary for structural component assembly. This work used novel covered laminas with co-cured joining techniques (CL-CCT) to create carbon fibre-reinforced polymer (CFRP) composite adhesive-bonded joints. Additionally, the researchers evaluated how multi-walled nanotubes (MWCNTs) affect bending dynamic properties of CFRP The added various weights MWCNTs along study revealed that epoxy 0.25 wt% MWCNT adhesive produced strongest most flexible These joints were 118 15% stronger made from pure CL-CC CFRP, respectively. Compared CC-CFRP joints, strength increased by 374 109%, Interestingly, a 1.25 had greatest natural frequency in all three vibration modes, which are 19, 13% higher joint. There 28, 30, 24% frequencies MWCNT-based those epoxy-based modes. Analysis variance was employed statistical investigation. Optimization prediction done using an artificial neural network Levenberg–Marquardt technique.
Language: Английский
Citations
7Hybrid Advances, Journal Year: 2024, Volume and Issue: 6, P. 100245 - 100245
Published: July 9, 2024
The synergistic effect of adding Silicon Carbide (SiC), Aluminum Oxide (Al2O3), and Graphene (GR) nanoparticles into Kevlar fiber-reinforced epoxy composites is investigated in this study. Within the matrix fibre reinforcement, these come a variety compositions. mechanical flammability features composite are revealed by experimental evaluation. Of nanoparticles, graphene performs best; reinforced with shows 324 MPa tensile strength, 8 J/mm impact 75.2 HRC hardness. layers' interior structure using scanning electron microscopy examination. To evaluate thermal stability composition thermogravimetric (TG) differential analysis (DTA) investigations were performed. Thermal achieved graphene-reinforced at 775 °C. Additionally, corrosion tests water absorption conducted to assess material's moisture sensitivity. overall goal research ascertain whether various produces best outcomes; has demonstrated promising results terms improving stability.
Language: Английский
Citations
5Polymer Composites, Journal Year: 2024, Volume and Issue: unknown
Published: Dec. 5, 2024
Abstract Cocured bonding and geometric modification are prominent techniques for fusing structural components in aerospace aircraft applications. This research involved the fabrication of carbon fiber‐reinforced polymeric (CFRP) adhesive‐bonded joints utilizing novel cocuring with interleaved lamination (IL‐CC) joining multiwalled nanotubes (MWCNTs) modified epoxy adhesive. Additionally, study examined flexural vibration characteristics IL‐CC CFRP composite joints. The result findings 1.0 wt% MWCNTs adhesive had best strength modulus, 78% 32% higher than pure exhibit a 285% 47% modulus neat CC Nevertheless, nanofiller 0.25 demonstrated highest natural frequency across three different modes, which 14%, 21%, 25% An ANOVA showed that MWCNT concentrations significantly influenced performance. Using Levenberg–Marquardt algorithm, an artificial neural network predicted results. overall coefficient ( R ) mean square error 0.99627 is satisfactory, indicating both outcomes dependable good agreement. results imply could be used parts. Highlights SLJs were fabricated MWCNT‐modified Attained maximum MWCNT. Statistics analyzed using one‐way technique. ANN predicts dynamic behavior SLJs.
Language: Английский
Citations
5Polymer Composites, Journal Year: 2025, Volume and Issue: unknown
Published: April 4, 2025
Abstract In recent years, there has been a lot of interest in the use natural fibers as reinforcements and ceramic particles fillers polymer composites. However, unoptimized process parameters frequently result flaws such cavity development, non‐homogeneous distribution, poor wettability, particle agglomeration. By optimizing filler %, stirring duration, number fiber layers, this study seeks to improve homogeneous distribution matrix reinforcement. This was accomplished by employing L 27 orthogonal array disperse silicon carbide (SiC) bamboo fiber‐reinforced epoxy The included varying SiC percentage (5%, 11%, 17%), duration (5, 10, 15 min), layers (2, 3, 4). order identify ideal parameter settings compare experimental results with predictions, utility analysis, conjunction an artificial neural network, utilized analyze response parameters, including porosity, inter laminar shear stress (ILSS), impact strength. According results, using 11% SiC, for 10 min, adding four increases strength 62.3% interlaminar 60.9% while lowering porosity 1.19%. These findings emphasize how crucial it is precisely manage processing optimize produce high‐performance composites improved mechanical characteristics few flaws. Highlights A drastic change ILSS from 12 18 MPa witnessed. Porosity dramatically decreased 2.5% after min swirling. Elongated were observed interaction region. Four increase 62.3%.
Language: Английский
Citations
0Polymer Composites, Journal Year: 2025, Volume and Issue: unknown
Published: April 9, 2025
Abstract The use of natural fibers as reinforcements in polymer composites has seen significant growth over recent decades. Despite their potential, these face limitations high‐temperature environments. To address this, ceramic particles like silicon carbide (SiC) can be introduced to enhance thermal stability and durability. This study investigates the impact SiC on mechanical characteristics woven bamboo fiber hybrid composites. By incorporating various weight fractions into an epoxy matrix, with three fiber/SiC layers were created using hand layup technique. comprehend synergistic impacts hybridization, mechanical, thermal, physical are used characterize generated samples. study's findings demonstrate that adding secondary reinforcement improves composites' qualities. Results indicate enhances tensile strength, flexural hardness by 33.9%, 13%, 5.8%, respectively. Additionally, thermogravimetric analysis (TGA) demonstrated properties improved increased content. Fracture analyses further revealed role reinforcing composites, making them suitable for both structural applications. Highlights reinforced 10% integration strength 33.9% 13%. 87.5 shore D was obtained during 20% integration. TGA witnessed enhanced rise confirmed excess aids crack nucleation.
Language: Английский
Citations
0