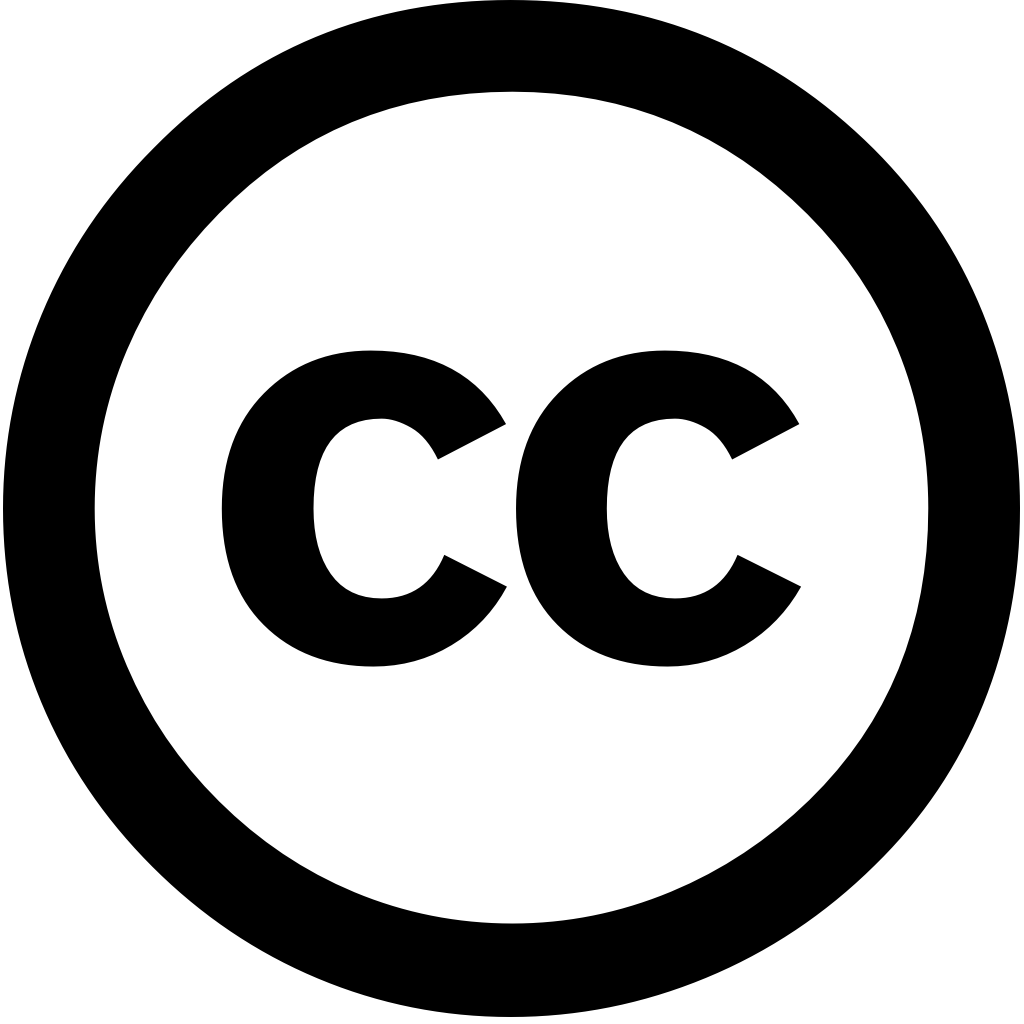
Journal of environmental chemical engineering, Journal Year: 2024, Volume and Issue: 12(5), P. 114067 - 114067
Published: Sept. 6, 2024
Language: Английский
Journal of environmental chemical engineering, Journal Year: 2024, Volume and Issue: 12(5), P. 114067 - 114067
Published: Sept. 6, 2024
Language: Английский
Separation and Purification Technology, Journal Year: 2024, Volume and Issue: 352, P. 128242 - 128242
Published: May 31, 2024
Language: Английский
Citations
10Advances in Colloid and Interface Science, Journal Year: 2025, Volume and Issue: unknown, P. 103487 - 103487
Published: March 1, 2025
Language: Английский
Citations
0Emergent Materials, Journal Year: 2025, Volume and Issue: unknown
Published: Feb. 4, 2025
Language: Английский
Citations
0Scientific Reports, Journal Year: 2024, Volume and Issue: 14(1)
Published: Feb. 28, 2024
Abstract The newest method for recycling waste linear low-density polyethylene (LLDPE) is the thermo-catalytic degradation technique known as catalytic pyrolysis. Typically, it limited by 500–800 °C high temperatures. Catalytic pyrolysis releases toxins and forms harmful carbonized char. current study based on exposing wasted LLDPE to different gamma irradiation doses then in castor oil (150–300 °C). output product of Ir-(rLLDPE) turned into another compound with a new structural architecture (sponge-like). SEM analysis confirms conversion, showing sponge-like spicules layers. soft, malleable, absorbent texture. DSC demonstrates altered thermal properties, melting point at 121 splitting two peaks (endothermic 117 exothermic 160 signify curing process material. assessed an adsorbent aqueous oils solvents. examines doses, temperature, time capacity. removal obeys Langmuir isotherm monolayer adsorption, maximum adsorption capacity 24.75 g/g 43 1,1,2,2-tetrachloroethane. Squashing maintains after 20 reuses. Data shows sponges effectively clean marine spills
Language: Английский
Citations
3International Journal of Environmental Science and Technology, Journal Year: 2024, Volume and Issue: unknown
Published: Aug. 30, 2024
Abstract This review deals with the applicability of polymeric sorbents in removing spilled free oil from water surfaces. The theoretical framework covers sorption ability materials general, respecting their size and morphology; however, main focus is on polyolefins, primarily various grades polyethylene (PE) polypropylene (PP), including PE PP waste. core motivation associated recycling LDPE low interest plastic convertors limited marketability these commodities. scientific this area development new products having at least two general features: i) a specific application that does not require high mechanical performance, ii) material has unique functionality significantly influenced by using recyclate against use pristine polymer. Recycled polyolefins fully satisfied requirements. pays special attention to aspects sorbents. Specific features are analyzed depending geometry morphology, involving powders, membranes/mats, 3D foams (sponges)/gels. wettability mechanisms regarding chemical composition materials, surface topology, internal porosity discussed detail. presented manuscript emphasizes close connection between materials’ behavior properties, which crucial for efficient oil/water separation modeling adsorption absorption processes. physical point view highlighted, enabling complex understanding
Language: Английский
Citations
2Processes, Journal Year: 2024, Volume and Issue: 12(8), P. 1542 - 1542
Published: July 23, 2024
One of the main challenges in treatment industrial wastewater is removal oil-in-water emulsions, which are stable and therefore difficult to treat. Bacterial cellulose (BC) has structural characteristics that make it an ideal filtration membrane. Several research projects underway develop new materials, both biotechnological traditional, for use filter beds. The study examined potential a BC membrane system treating oily wastewaters, underexplored biomaterial treatment. results demonstrated highly effective at removing contaminants (~99%), reducing colour particulate matter wastewater, as well eliminating nearly entire microbiological load (~99%). SEM, MEV, FTIR, XRD, TGA confirmed presence oil interior after filtration, characteristic peaks its chemical composition, 40% reduction crystallinity. revealed increase from three (pre-filtration) five (post-filtration) stages thermal degradation, indicating retention contaminant BC. mechanical tests tensile strength 72.13 ± 8.22 MPa tolerated elongation up 21.11 4.81% prior tearing. also exhibited excellent flexibility, could be folded >100 times same point without exhibiting signs surpasses traditional methods, such activated charcoal effluent stations, emulsified oils. findings demonstrate promising field requires continual technological innovations mitigate environmental impacts industry.
Language: Английский
Citations
1Journal of environmental chemical engineering, Journal Year: 2024, Volume and Issue: 12(5), P. 114067 - 114067
Published: Sept. 6, 2024
Language: Английский
Citations
0