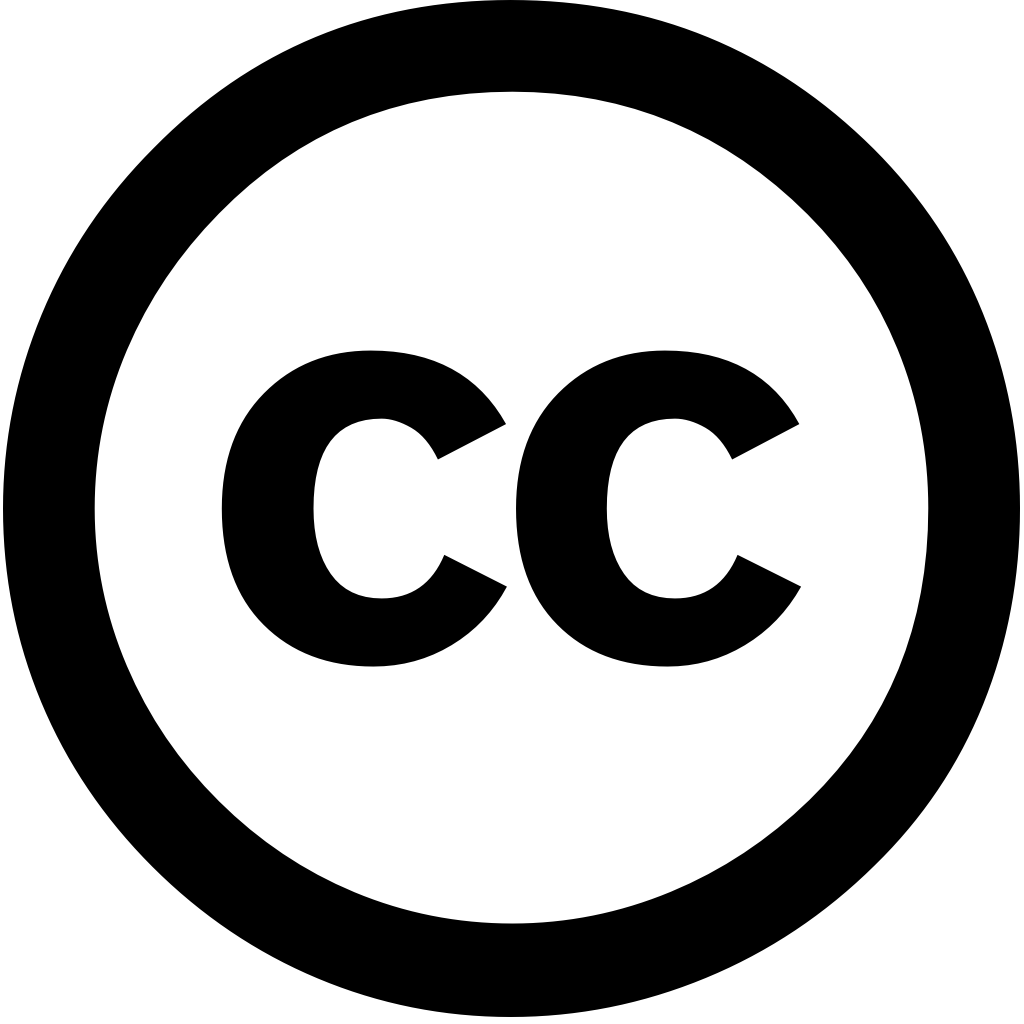
Journal of Machine Engineering, Journal Year: 2024, Volume and Issue: 24(4), P. 1 - 12
Published: Nov. 22, 2024
Abstract: Trajectory path generation is critical for the Autonomous Mobile Robot (AMR) when moving frequently in working environment shop floor to transport loads from one work station another continuously. Traditionally, AMR moves point stop at next or turn which inefficient and consumes much energy. This paper proposes new concept of trajectory planning with curvature driven by maximizing speed control differential drive each curve move smoothly. B-splined commonly applied CAD CAM machining effectively tool trajectory. Therefore, studied validated simulation together energy consumption. The on Matlab Simulink numerical model. It investigated that efficient animating AMR’s actual system. velocity can obtain both linear angular movements forward backward directions as well acceleration. be selected based degree closeness used generate
Language: Английский