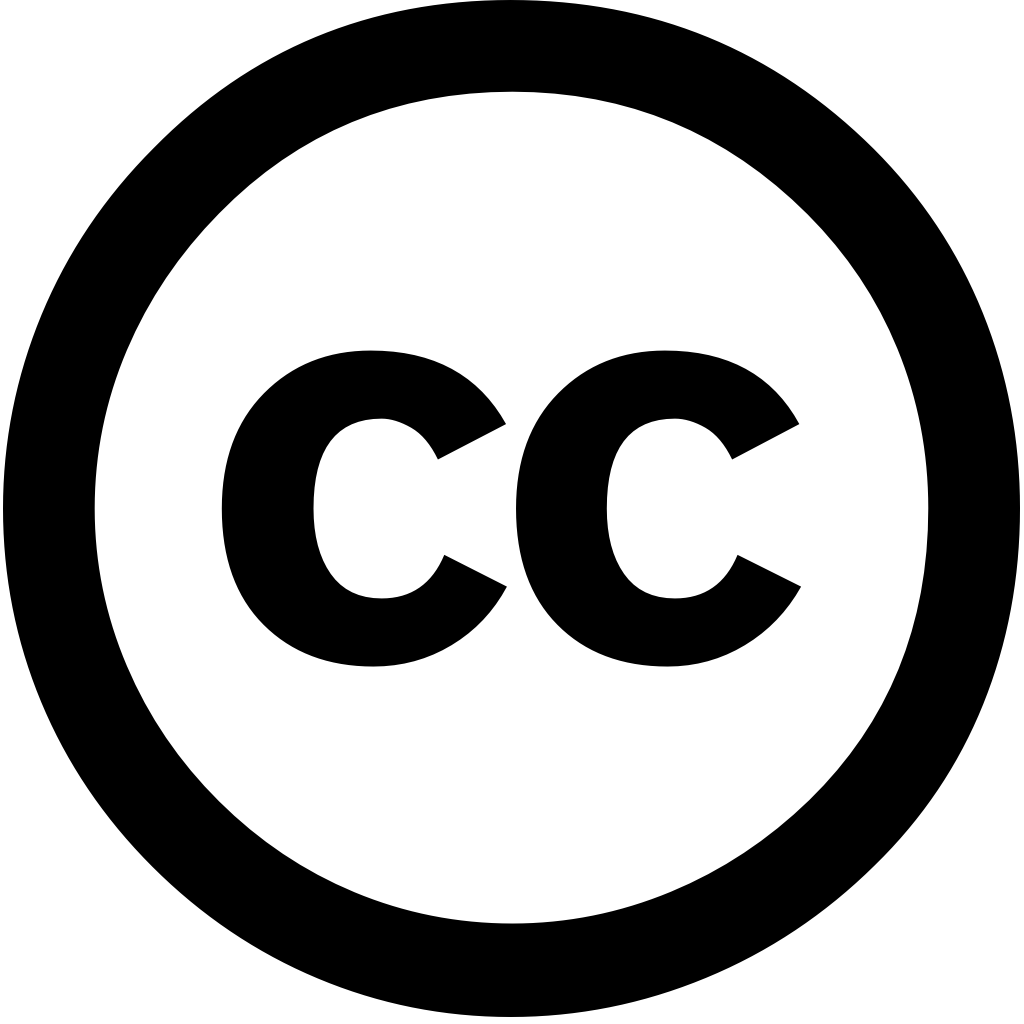
Thin-Walled Structures, Journal Year: 2024, Volume and Issue: unknown, P. 112848 - 112848
Published: Dec. 1, 2024
Language: Английский
Thin-Walled Structures, Journal Year: 2024, Volume and Issue: unknown, P. 112848 - 112848
Published: Dec. 1, 2024
Language: Английский
Composites Science and Technology, Journal Year: 2024, Volume and Issue: 253, P. 110632 - 110632
Published: April 26, 2024
Language: Английский
Citations
16Composites Part A Applied Science and Manufacturing, Journal Year: 2024, Volume and Issue: 182, P. 108171 - 108171
Published: March 26, 2024
Language: Английский
Citations
13Thin-Walled Structures, Journal Year: 2024, Volume and Issue: 203, P. 112203 - 112203
Published: July 6, 2024
Language: Английский
Citations
7Journal of Elastomers & Plastics, Journal Year: 2025, Volume and Issue: unknown
Published: Jan. 14, 2025
This paper investigates the compression-tested mechanical properties of 3D Polylactic acid (PLA) printed Triply Periodic Minimal Surfaces (TPMS) lattice structures, exploring impact varying input parameters. The parameters included in this study are cellular structure, printing speed, and unit cell size. serves as a valuable guide for achieving specific through selection optimal three would have major effect overall specimens. Four output were studied experiment elastic modulus, yield stress, plateau toughness. A Desirability Function Analysis (DFA) was implanted to achieve most parameter combination it compared original By comparing nine samples against predicted optimized parameter, toughness increased by 2.15%, modulus 108.33%, stress 4% 3.97%.
Language: Английский
Citations
0International Journal of Mechanical Sciences, Journal Year: 2025, Volume and Issue: unknown, P. 110063 - 110063
Published: Feb. 1, 2025
Language: Английский
Citations
0International Journal of Mechanical Sciences, Journal Year: 2024, Volume and Issue: 284, P. 109771 - 109771
Published: Oct. 8, 2024
Language: Английский
Citations
2International Journal of Smart and Nano Materials, Journal Year: 2024, Volume and Issue: 15(4), P. 786 - 810
Published: Oct. 1, 2024
Triply periodic minimal surface (TPMS) structures with excellent properties of stable energy absorption, light weight, and high specific strength could potentially spark immense interest for novel programmable functions by combining smart materials, e.g. shape memory polymers (SMPs). This work proposes TPMS lattices hybrid configurations materials that are composed viscoelastic shape-memory the aim to bring temperature-dependent mechanical additional dissipation mechanisms. Different diverse polylactic acid (PLA), fiber-reinforced PLA, polydimethylsiloxane (PDMS) induced, generating five types lattices, including (Schoen's I-WP) IWP uniform lattice, lattice density gradient, configurations, filled PDMS, which fabricated 3D printing. The fracture morphologies distribution carbon fibers demonstrated via scanning electron microscopy a focus on influence fiber properties. Shape recovery tests conducted, proves good reusable capability lattice. combined methods experiments numerical simulation adopted evaluate properties, presents multi-stage absorption ability tunable vibration isolation performances associated temperature hybridization designs. can promote extensive research provide substantial opportunities in development functional applications.
Language: Английский
Citations
1Advanced Engineering Materials, Journal Year: 2024, Volume and Issue: unknown
Published: Nov. 7, 2024
Designing structures that effectively dissipate energy across a broad range of mechanical loading rates, including those from compression, shock, and vibration, poses significant engineering challenge. In this study, liquid‐crystal elastomers (LCEs), which possess anisotropic properties due to the alignment their polymer backbone, are explored. As result, LCEs exhibit soft elastic response under loading, making them ideal for dissipation. Advances in additive manufacturing (AM) enable simple fabrication foamlike dissipative with complex lattice geometries. Herein, direct ink write 3D printing, an extrusion AM method, is used fabricate aligned, monodomain LCE strain‐rate damping. work, it shown these can strain quasi‐static environments, comparable traditional elastomeric lattices, provide improved damping high drop testing elasticity. Additionally, dynamic lattices enhance at structural natural frequencies high‐frequency attenuation. findings, promising method presented fabricating devices rates.
Language: Английский
Citations
1Thin-Walled Structures, Journal Year: 2024, Volume and Issue: unknown, P. 112847 - 112847
Published: Dec. 1, 2024
Language: Английский
Citations
1Advanced Engineering Materials, Journal Year: 2024, Volume and Issue: unknown
Published: Oct. 31, 2024
Herein, a novel material design strategy is proposed: an interpenetrating composite composed of woven orthogonal spiral metal skeleton and polyurethane (PU) elastomer. This combines rigidity flexibility, exhibiting excellent elasticity deformation recovery. The behavior mechanical properties the composites under various loading conditions are investigated through experiments numerical simulations. Different degrees warping behaviors occur in with structural parameters uniaxial tension. Alternating rotations double arrangements can significantly limit phenomenon, maximum reduction 78%. bending load capacity regularly increased by increasing wire diameter decreasing pitch. Increasing number loaded wires enhances composites. Uniaxial compression tests demonstrate that have load‐carrying strain recovery, compressive strength 1.5 times pure PU. Cyclic further illustrate energy consumption stability Overall, introduction skeletons into demonstrates potential to achieve enhanced large recovery simultaneously.
Language: Английский
Citations
0