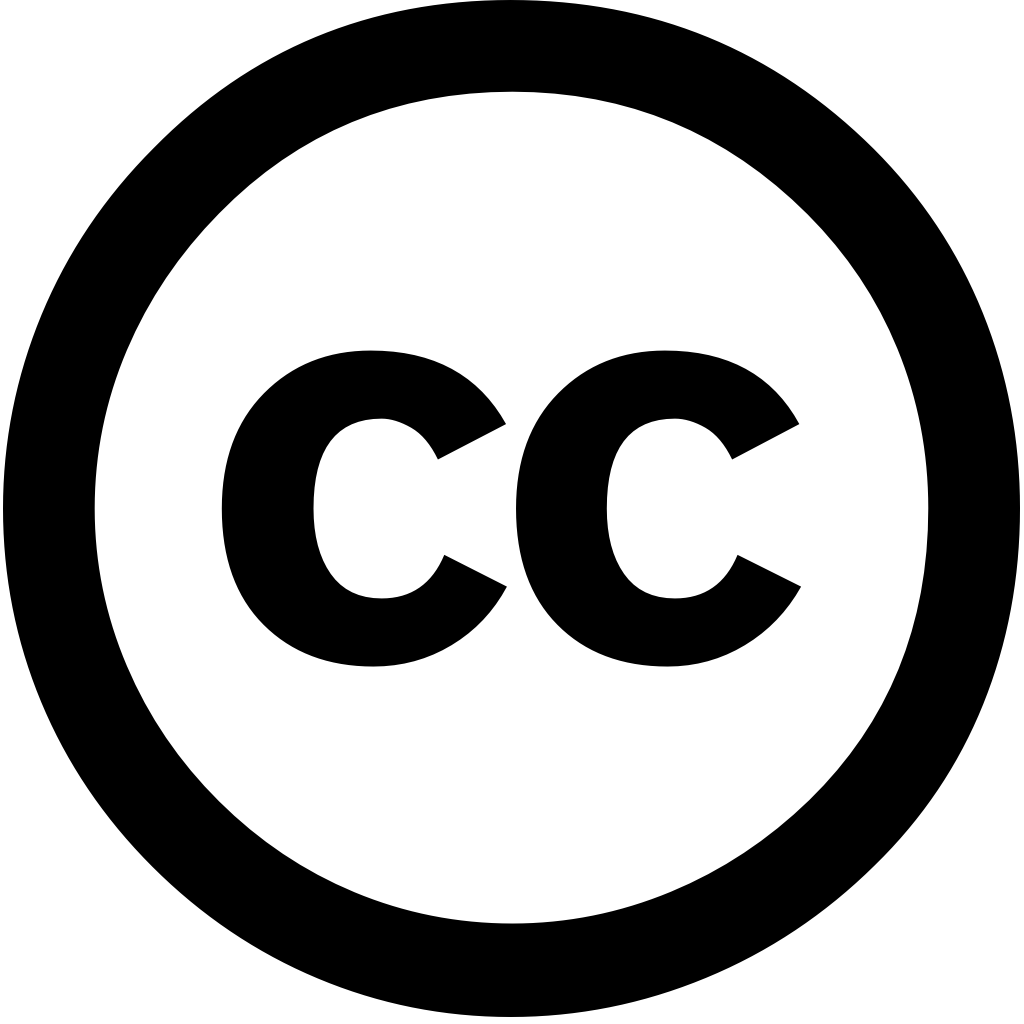
Ultrasonics Sonochemistry, Journal Year: 2025, Volume and Issue: unknown, P. 107330 - 107330
Published: March 1, 2025
This study demonstrates a rapid and facile method for separating the central membrane catalyst-coated material from production scrap fuel cell membranes (CCMs), facilitating circular economy of technologically critical metals. A novel approach is presented using high-intensity ultrasonication with two distinct sonotrode configurations delamination at ambient temperature in water. technique utilises cavitation, where high-frequency sound waves create, expand, collapse microbubbles, generating high-speed jets, shockwaves, acoustic streaming. process effectively separates catalyst while maintaining their overall integrity former. cylindrical (20 mm diameter) was used to optimise parameters smaller CCM samples minimise time energy consumption. To scale up industrial-size CCMs, blade (15 x 210 mm) employed enable flow continuous delamination. Cavitation sonotrode-CCM interface shown facilitate selective breakdown layers, enabling full catalyst-loaded within tens seconds. efficient fast offers promising strategy recycling.
Language: Английский