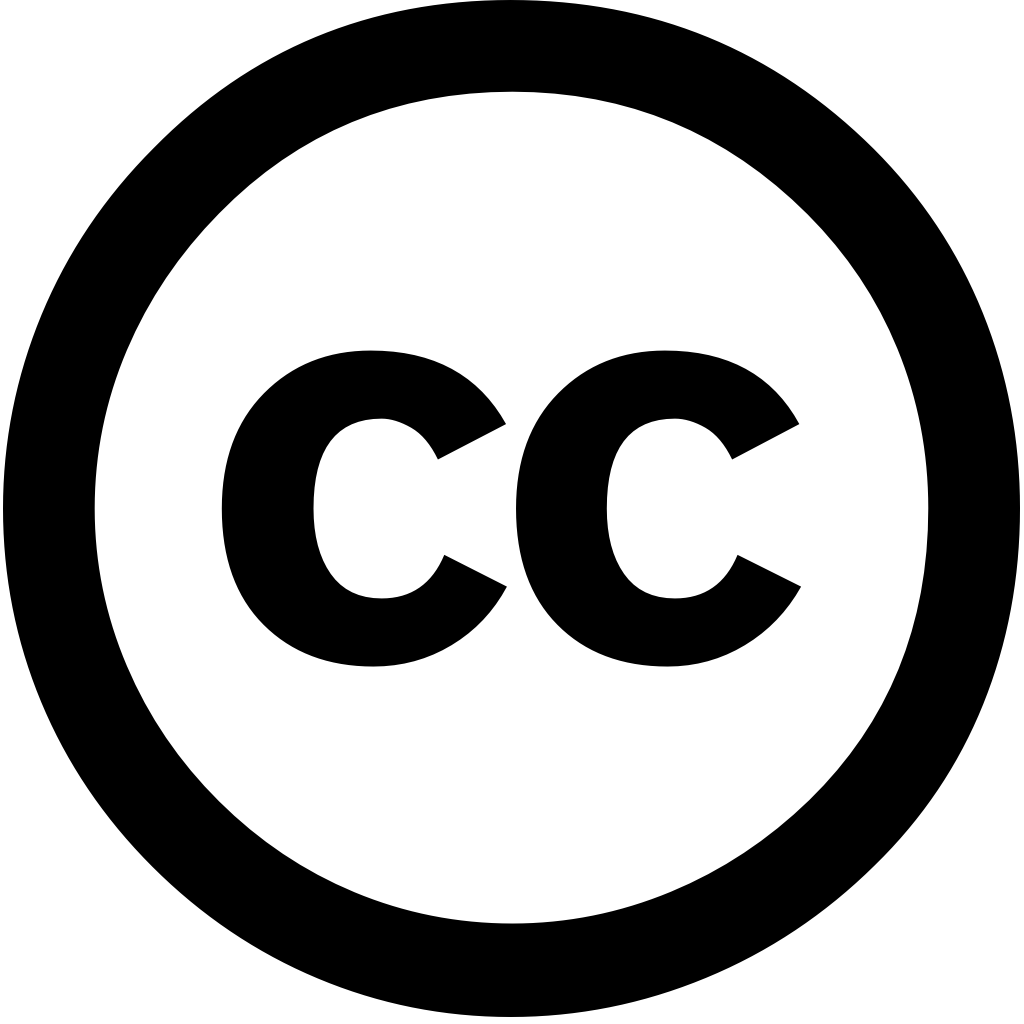
Agriculture, Journal Year: 2025, Volume and Issue: 15(5), P. 557 - 557
Published: March 6, 2025
Combined with the characteristic that tea is generally planted in hilly and mountainous areas considering existing problems of harvesting current pickers, such as inability to adjust their posture real time, poor adaptability terrain, insufficient stability, large differences lengths tea. To address these issues, an adaptive canopy-following cutting control system has been designed for self-propelled harvesters this study. Specifically, we developed a height-following algorithm canopy tracking header tilt angle based on incremental PID control. Field experiments demonstrated when vehicle speed was 0.4 m/s, height errors three (20 mm, 30 40 mm) remained within ±5 correlation coefficients exceeding 0.99. When between two sides ridge were 10 cm, 15 20 maximum uphill roll angles measured at 1.7°, 2.3°, 3.0°, respectively, time taken harvester return horizontal position around 1.7 s. During downhill movement, 1.3°, 2.0°, 2.6°, 2.1 s, demonstrating significant correction effectiveness. Quality assessments revealed mm length specification, integrity rate exceeded 79%, while missed below 1.1%. This effectively enhances stability quality, offering novel insights efficient, high-volume production.
Language: Английский