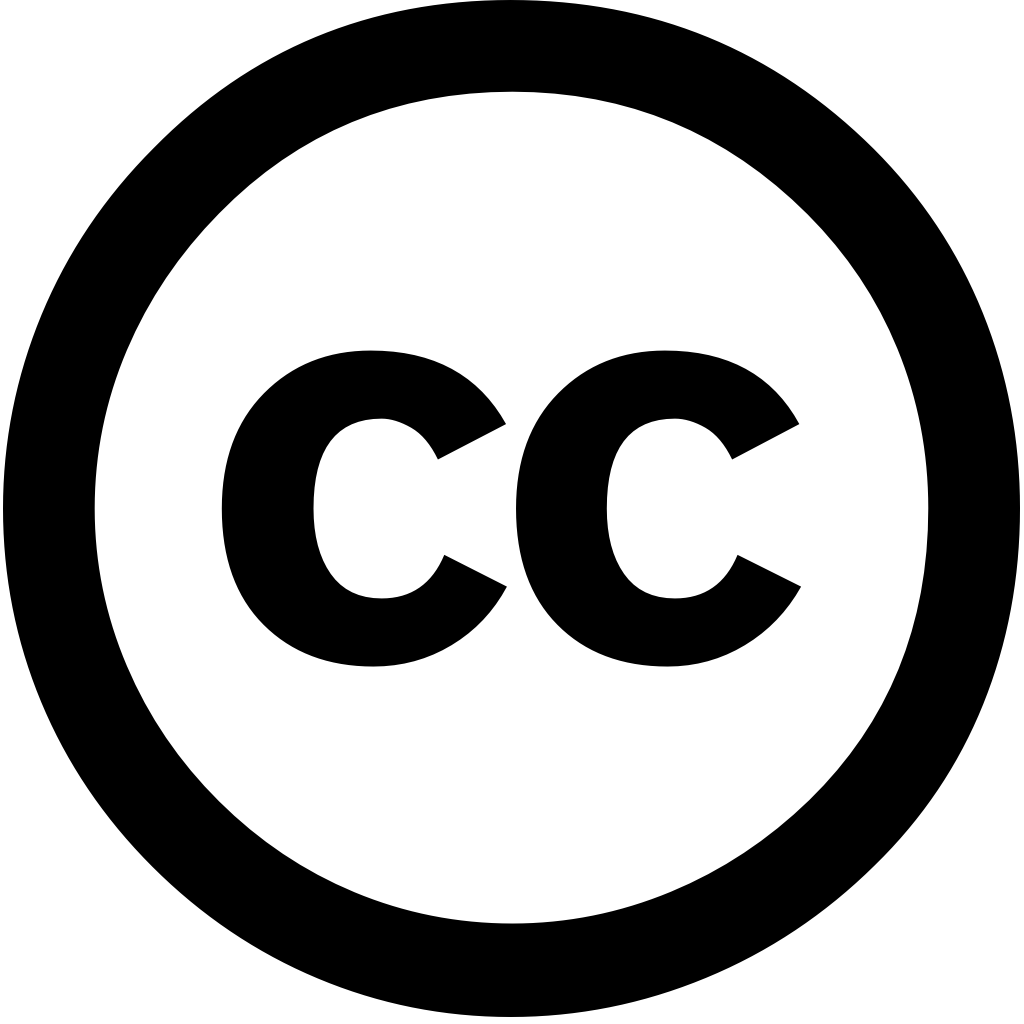
Micromachines, Journal Year: 2025, Volume and Issue: 16(4), P. 391 - 391
Published: March 28, 2025
For Measurement While Drilling (MWD), the redundant Micro-Electro-Mechanical Systems Inertial Unit (MEMS-IMU) navigation system significantly enhances reliability and accuracy of drill string attitude measurements. Such an enhancement enables precise control wellbore trajectory overall quality drilling operations. But installation errors MEMS-IMUs still degrade It is essential to calibrate these ensure measurement precision. Currently, commonly used calibration method involves mounting carrier on a horizontal plane performing through rotation. However, when rotates plane, gravity acceleration component sensed by axis IMU accelerometer in very small, which leads low signal-to-noise ratio, so that measured matrix obtained solution dominated noise. As result, insufficient, and, finally, effectiveness error compensation reduced. In order solve this problem, study proposes 45°-inclined six-position based selected hexagonal prism structure for MWD. Firstly, matrices were analyzed, new was proposed; IMUs should be installed at inclined position 45°. Then, six measuring points identified proposed approach. Finally, simulation laboratory experiments conducted verify method. The results showed reduced 40.4% compared with conventional methods. experiments’ demonstrated reductions 83% 68% absolute x y axes, respectively. sensor after improved over 25% traditional effectively improves systems, providing approach downhole trajectories.
Language: Английский