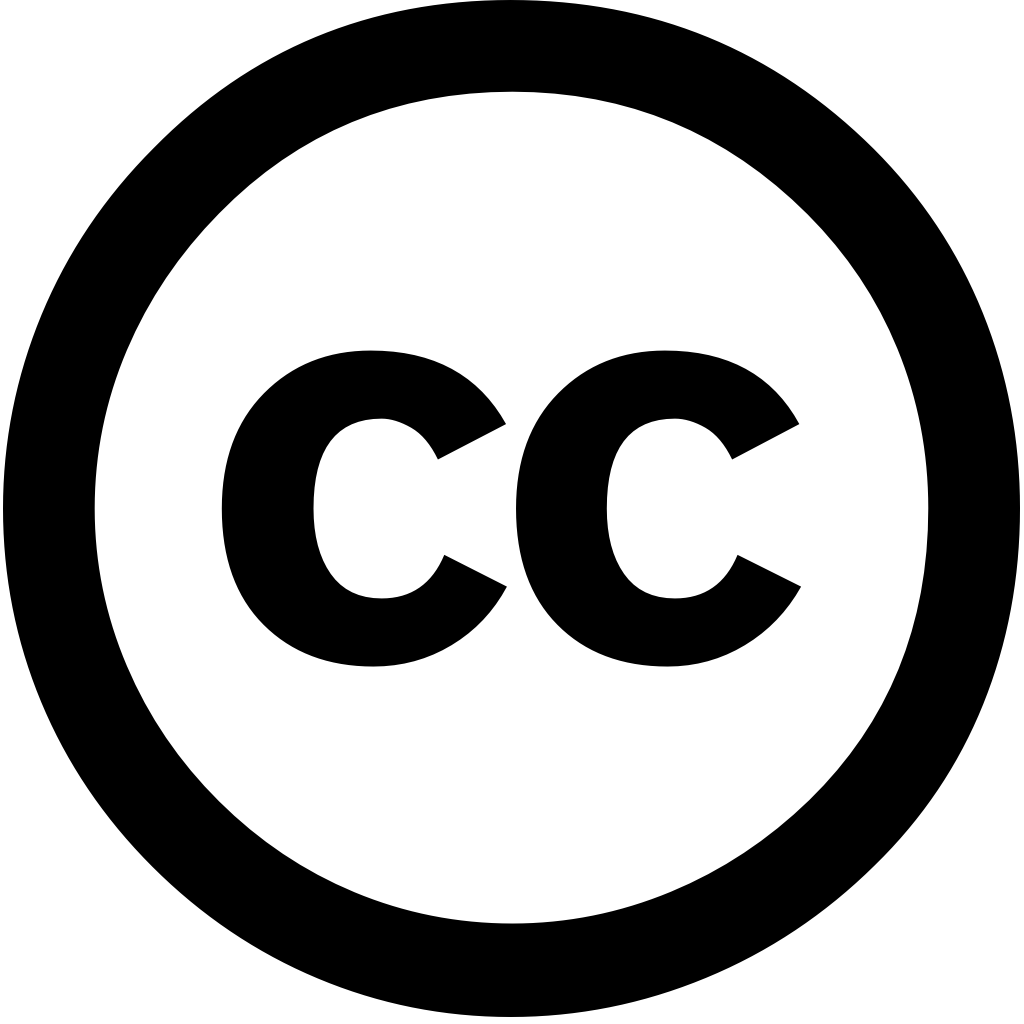
Energies, Journal Year: 2025, Volume and Issue: 18(8), P. 2099 - 2099
Published: April 18, 2025
Turbines are rotating machines that generate power by the expansion of a fluid; due to their characteristics, these turbomachines widely applied in aerospace propulsion systems. Due clearance between rotor blade tip and casing, there is leakage flow from pressure suction sides, which generates energy loss. There different strategies can be avoid part this loss; one them application so-called desensitization techniques. The techniques on gas turbines has been evaluated; however, lack analyses hydraulic turbines. This study continuation earlier conducted during first stage axial turbine used low-pressure oxidizer turbopump (LPOTP) space shuttle main engine (SSME). previous work analyzed squealer geometries at tip. In present paper, winglet geometry investigated based three-dimensional flowfield calculations. commercial CFX v.19.2 ICEM software were used, respectively, numerical simulations computational mesh generation. Experimental results published National Aeronautics Space Administration (NASA) data works model validation. parametric analysis was varying thickness width winglet. obtained show increasing thickness, efficiency also increased. However, geometric dimension its minimal impact result. An average increase 2.0% observed across entire operational range. case squealer, for design point, maximum improvement 1.62%, compared current 2.23% using technique. It found proposed changes cavitation occurrence along stage, relevant result, since it life cycle.
Language: Английский